Carbon nanofibers hold great technological importance for a variety of high-performance applications. Due to their exceptional properties including being lightweight, having high electrical conductivity, thermal stability, and excellent mechanical properties, they are being used in a wide range of applications including energy, catalysis, and aerospace. Polyacrylonitrile (PAN) is a synthetic polymer resin that is used to produce about 90% of commercial carbon fibers today [1]. Electrospinning can fabricate PAN nanofibers as small as 100 nm in diameter. PAN fibers can then be processed through a series of heat treatments to form carbon nanofibers. This process can be scaled to fabricate carbon nanofibers in large enough quantities to meet the needs of industrial applications.
Carbon Nanofibers:
Carbon fibers have various benefits, making them a highly sought-after material across various industries. Inherent to carbon fiber materials, they possess high tensile strength, are electrically conductive, lightweight, and resistant to degradation and corrosion. In energy storage applications, carbon fibers are utilized to improve the performance of lithium-ion battery anodes, supercapacitors, and dye-sensitized solar cells [1-2]. The high tensile strength and lightweight properties of carbon fiber are leveraged in the aerospace and automotive industries to provide durable frameworks and improved fuel efficiency [3]. Carbon fiber-reinforced polymers are also making their way into the medical device industry to replace the standard metallic implants [4]. Construction of bridges, buildings, and wind turbines incorporate carbon fiber in the building materials due to their high strength and lightweight properties. There is an increasing trend towards developing carbon fibers in the sub-micrometer diameter range. Due to their high surface area, these so-called nanofibers hold promise for several emerging applications including energy conversion and storage, catalysis, and filtration.
Polyacrylonitrile (PAN):
PAN is a thermoplastic polymer that is composed of repeating units of acrylonitrile, (C3H3N) and is the most used precursor of carbon fibers. Compared to other precursors for carbon fibers, PAN-derived synthesis results in higher carbon yields and better mechanical properties. PAN resins are typically copolymeric, containing small fractions of other monomers that enhance the properties of the produced carbon fibers. PAN-derived or PAN-based carbon fibers are made by a variety of methods wherein a PAN solution is extruded into highly viscous one-dimensional fibers [1]. These fibers are then stabilized under controlled heating, usually around 200-300°C, and finally carbonized within an inert atmosphere at temperatures exceeding 1000°C. In traditional approaches, the typical fiber size range is a few microns up to tens of micrometers.
Although there are many advantages to carbon fiber, the micron-sized fibers have limited flexibility and produce a brittle material. Nanofibers of carbon can overcome some of these limitations, especially with improved material flexibility [5]. Furthermore, the nanofibrous structures have a high surface area-to-volume ratio. The high surface area improves ion transfer efficiency within energy applications, provides good support for catalysis, and improves the energy density of supercapacitors [1]. Carbon nanofibers are commonly developed via chemical vapor deposition or vapor growth method. However, these processes are highly complex and costly to implement [6]. Other options are required to improve the cost efficiency of nanofiber production. Electrospinning is a promising approach that can fabricate carbon nanofibers in a cost-effective and efficient process.
Fabricating PAN Nanofibers with Electrospinning
Compared to conventional fabrication methods, electrospinning relies on the application of an electrical field to fabricate fibers from a polymer solution. During the electrospinning process, a dissolved polymer solution is extruded into a highly charged electric field and is propelled toward a grounded or negatively charged collector. During the time of flight, the solvents evaporate, and the polymer is collected in the form of a nanofiber sheet (Figure 1).
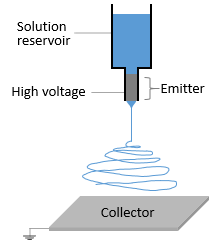
The electrospinning parameters can be tuned to control fiber alignment in a random, semi-aligned, or aligned orientation [7]. Furthermore, the solution formulation can be optimized for generating electrospun fibers that range from 100 nm to a few microns. Utilizing electrospinning will result in the production of PAN nanofiber mats in a single step with tunable fiber diameters, fiber orientations, and mat thicknesses. The electrospinning process can subsequently be scaled up in production to meet the needs of commercial applications.
Carbonization of PAN Fibers
Once the PAN fiber mat is fabricated, arguably the most important step in producing carbon nanofibers with desirable properties is the carbonization process. The goal of carbonization is to convert the precursor material into high-strength carbon nanofibers through multiple carefully optimized heat treatments (Figure 2). The heating rate, temperature, as well as gas flow rates all play an important role in determining the final properties of the carbon fibers.
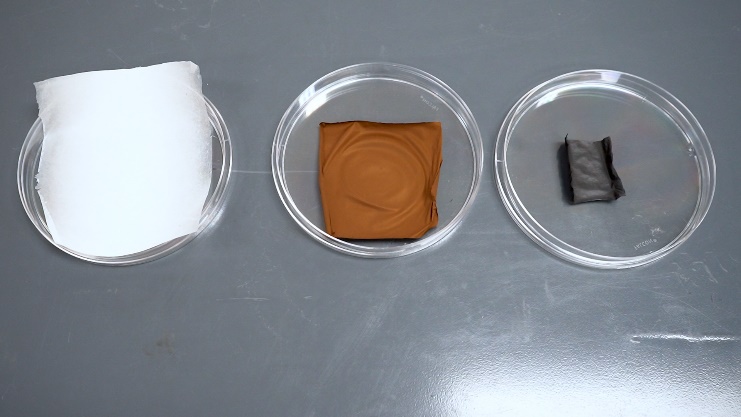
Before carbonization, a heat treatment known as oxidative stabilization is carried out to promote cross-linking of PAN macromolecular chains. Usually, PAN nanofibers are heated between 200°C to 300°C under ambient conditions to achieve this effect through oxidation, cyclization, and dehydrogenation [1,8]. At this point, the stabilized PAN nanofibers are more resistant to melting, which could fuse the fibers. This step also minimizes the volatilization of carbon atoms during subsequent carbonization steps, thereby maximizing carbon yield.
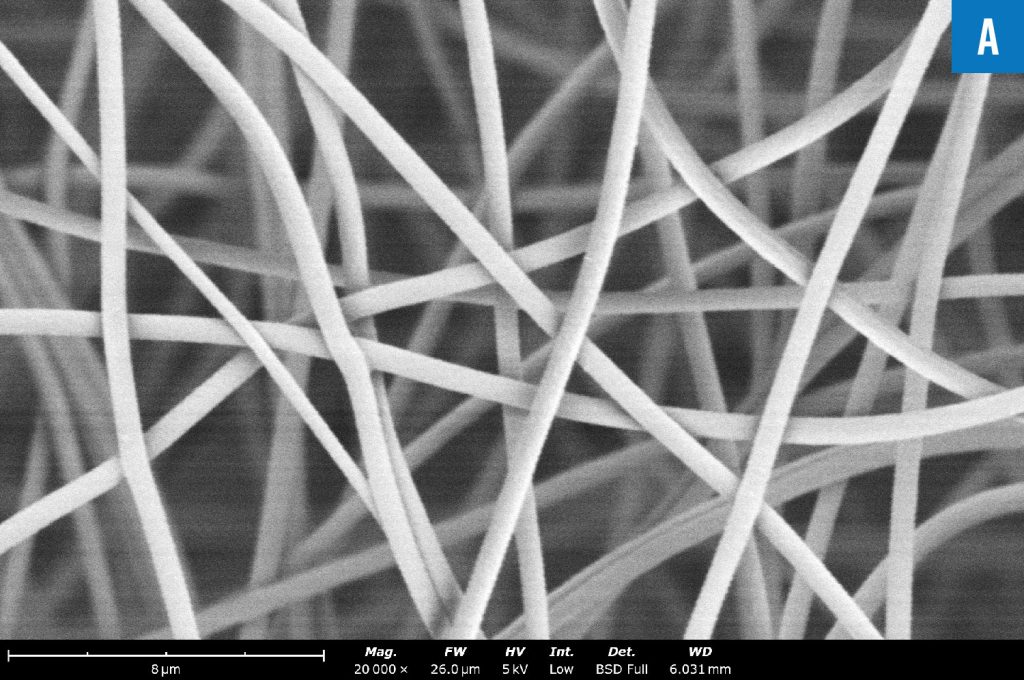
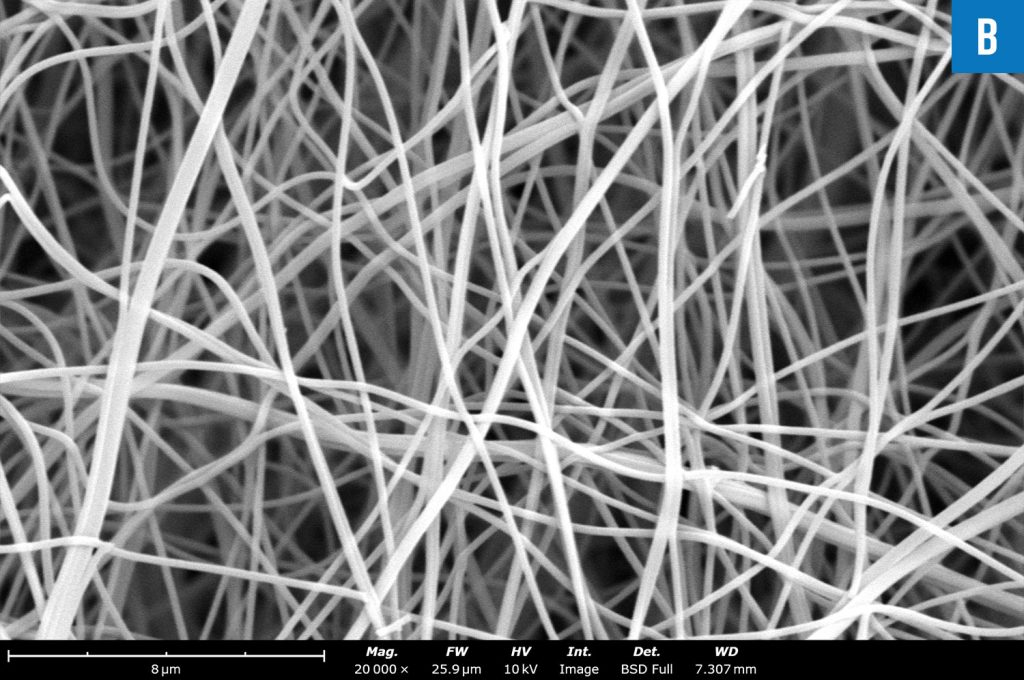
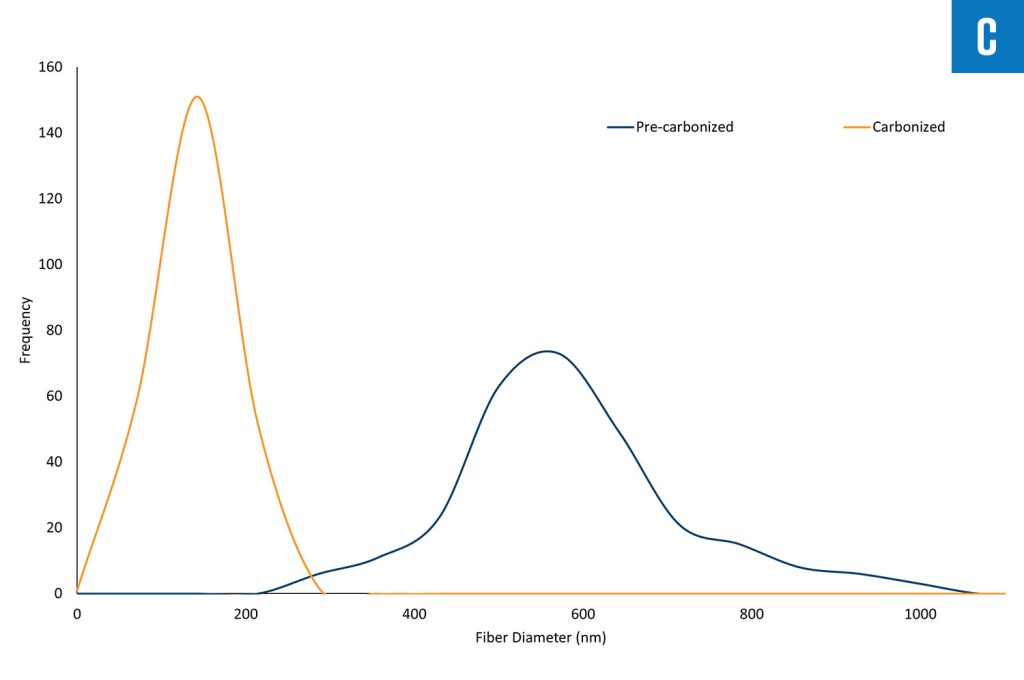
Following stabilization, carbonization is performed under an inert atmosphere, usually in nitrogen or argon, to eliminate all non-carbon atoms. Carbonization heat treatment usually involves progressively heating the nanofibers to 1000°C then allowing them to cool slowly [1,9]. Non-carbon atoms become volatilized into a variety of gases while the fiber diameter reduces because of the mass loss. Maintaining proper gas flow and ventilation during carbonization ensures that hazardous gases, such as methane and ammonia, are properly removed from the environment. The structural transformation from a disordered carbon structure to a graphitic phase can also take place at higher temperatures, resulting in enhanced mechanical strength. Due to the removal of the initial PAN contents, after the carbonization process, the fibers are shown to decrease in fiber diameter (Figure 3). From pre-carbonized to carbonized, the average fiber diameter decreased from 620 ± 130 nm (Figure 3A) to 194 ± 52 µm (Figure 3B). Furthermore, the removal of PAN contents throughout the heat-treated steps changes the surface wettability of the fiber mat. Pre-carbonized PAN fibers led to a hydrophilic contact angle of nearly 40o (Figure 4A). Post-treated mats led to a highly hydrophobic surface with a contact angle near 150o (Figure 4B). Producing a highly hydrophobic nanofiber mat leads to excellent resistance to corrosion and moisture damage. The corrosion-resistant properties generated by the hydrophobic surface are critical for the aerospace, energy, and automotive industries. By changing the surface wettability properties, electrospun PAN nanofibers were successfully processed into carbon nanofibers that can be used for a variety of applications.
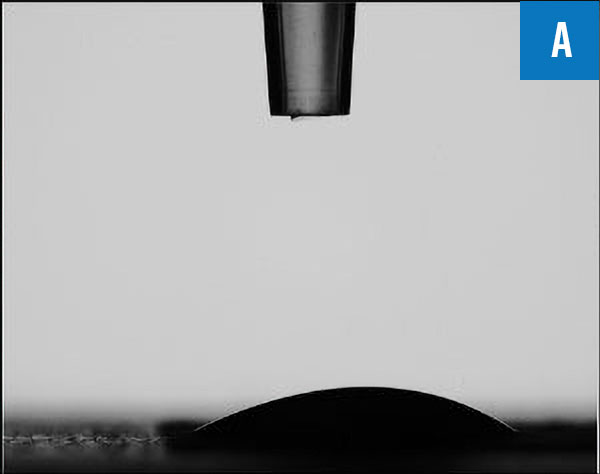
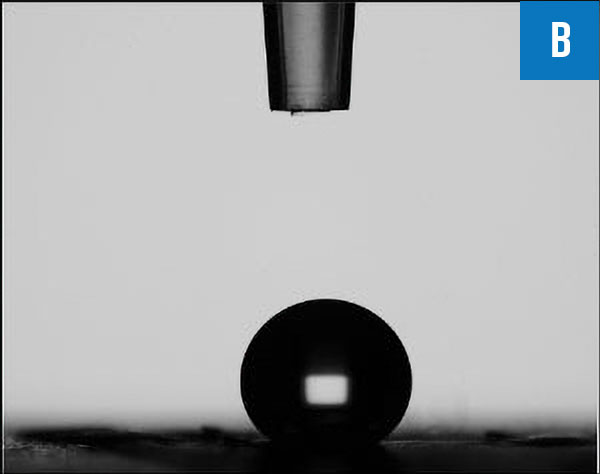
Conclusion
PAN-derived carbon nanofibers are a highly versatile and widely used material in modern industry. Their excellent mechanical, thermal, and electrical properties make them suitable for a wide range of applications. The production process involves electrospinning PAN into a fiber and then carbonizing it under controlled conditions. The applications of PAN-derived carbon nanofibers primarily include aerospace, energy conversion and storage.
References
[1] L. Zhang, A. Aboagye, A. Kelkar, C. Lai and H. Fong, “A review: carbon nanofibers from electrospun polyacrylonitrile and their applications,” Journal of Materials Science, vol. 49, pp. 463-480, 2014.
[2] G. Lim, K. Chan, N. Sutrisnoh and M. Srinivasan, “Design of structural batteries: carbon fibers and alternative form factors,” Materials Today Sustainability, vol. 20, p. 100252, 2022.
[3] Zheng, H., Zhang, W., Li, B., Zhu, J., Wang, C., Song, G., … & Ma, L. (2022). Recent advances of interphases in carbon fiber-reinforced polymer composites: A review. Composites Part B: Engineering, 233, 109639.
[4] Chua, C. Y. X., Liu, H. C., Di Trani, N., Susnjar, A., Ho, J., Scorrano, G., … & Grattoni, A. (2021). Carbon fiber reinforced polymers for implantable medical devices. Biomaterials, 271, 120719.
[5] Yang, X., Chen, Y., Zhang, C., Duan, G., & Jiang, S. (2023). Electrospun carbon nanofibers and their reinforced composites: Preparation, modification, applications, and perspectives. Composites Part B: Engineering, 249, 110386.
[6] Gu, S. Y., Ren, J., & Vancso, G. J. (2005). Process optimization and empirical modeling for electrospun polyacrylonitrile (PAN) nanofiber precursor of carbon nanofibers. European polymer journal, 41(11), 2559-2568.
[7] Tindell, R. K., Busselle, L. P., & Holloway, J. L. (2023). Magnetic fields enable precise spatial control over electrospun fiber alignment for fabricating complex gradient materials. Journal of Biomedical Materials Research Part A, 111(6), 778-789.
[8] A. F. I. Norhaniza Yusof, “Post spinning and pyrolysis processes of polyacrylonitrile (PAN)-based carbon fiber and activated carbon fiber: A review,” Journal of Analytical and Applied Pyrolysis, vol. 93, pp. 1-13, 2011.
[9] M. Salahuddin, M. N. Uddin and G. Hwang, “Superhydrophobic PAN nanofibers for gas diffusion layers of proton exchange membrane fuel cells for cathodic water management,” International Journal of Hydrogen Energy, vol. 43, no. 25, pp. 11530-11538, 2018.